In our daily work routine, we are confronted from time to time with situations that virtually “request” a bit of rethinking. Things that have always been done this way and have never really been questioned, but now seem far too laborious and simply no longer right for a variety of reasons. Since the topics of resource conservation and sustainability are close to our hearts, the following case exactly represents such a situation:
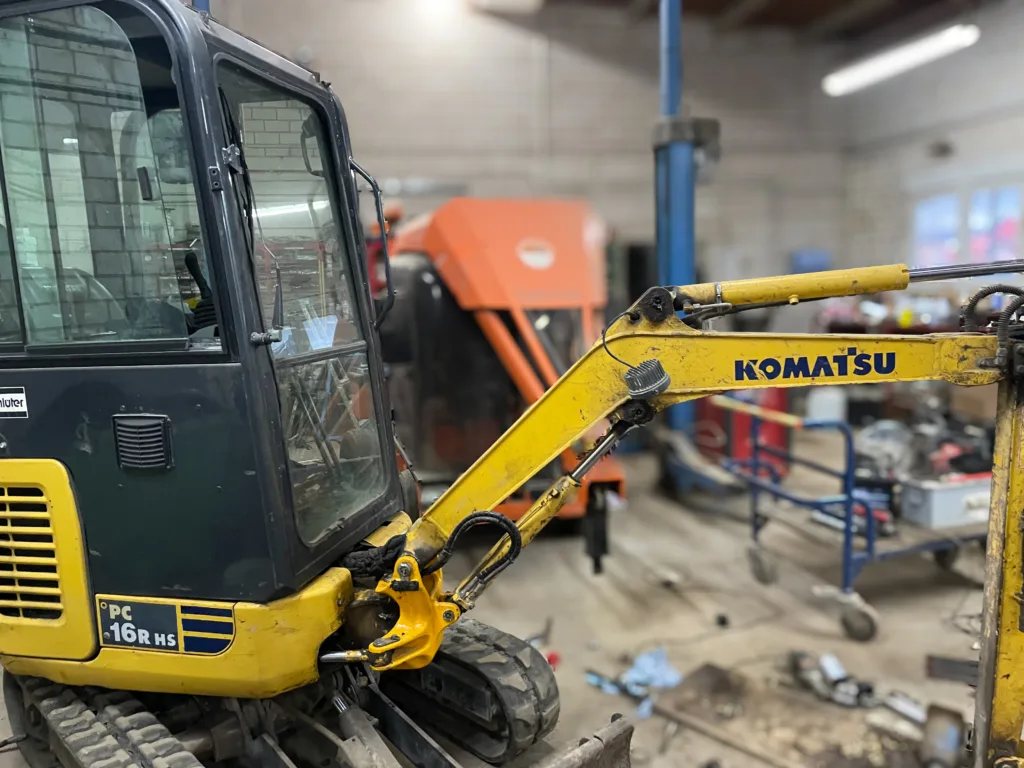
The swing frame of a Komatsu mini-excavator, spare part comparison number 22J-70-R5410, suitable for models PC14 and PC16, was worn out and we were given the task of getting a corresponding spare part. The problem with this – and after all the point that spurred us to action: These components are made in Asia, so they have to be shipped halfway around the world to get to us; they’re made entirely of steel, and one part weighs about 20 kg. So the whole thing is incredibly resource-intensive and ultimately, of course, correspondingly expensive.
This is why we asked ourselves how this issue could be solved or at least simplified, but were soon faced with the challenge that this part itself cannot be repaired at all, as it consists of one cast-iron piece of steel with holes simply drilled into it. Since the entire boom/arm of the excavator hangs on this mount and it is therefore exposed to a correspondingly high stress, the bushings are worn out after a short time and the part is no longer usable. Result: it has to be replaced.
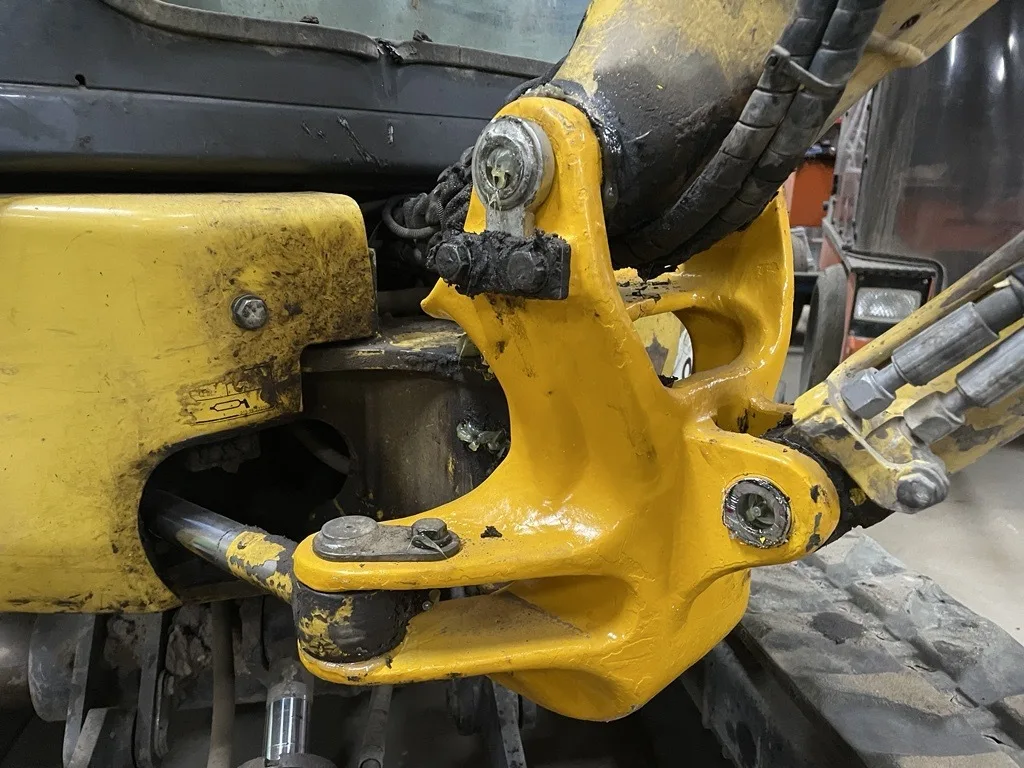
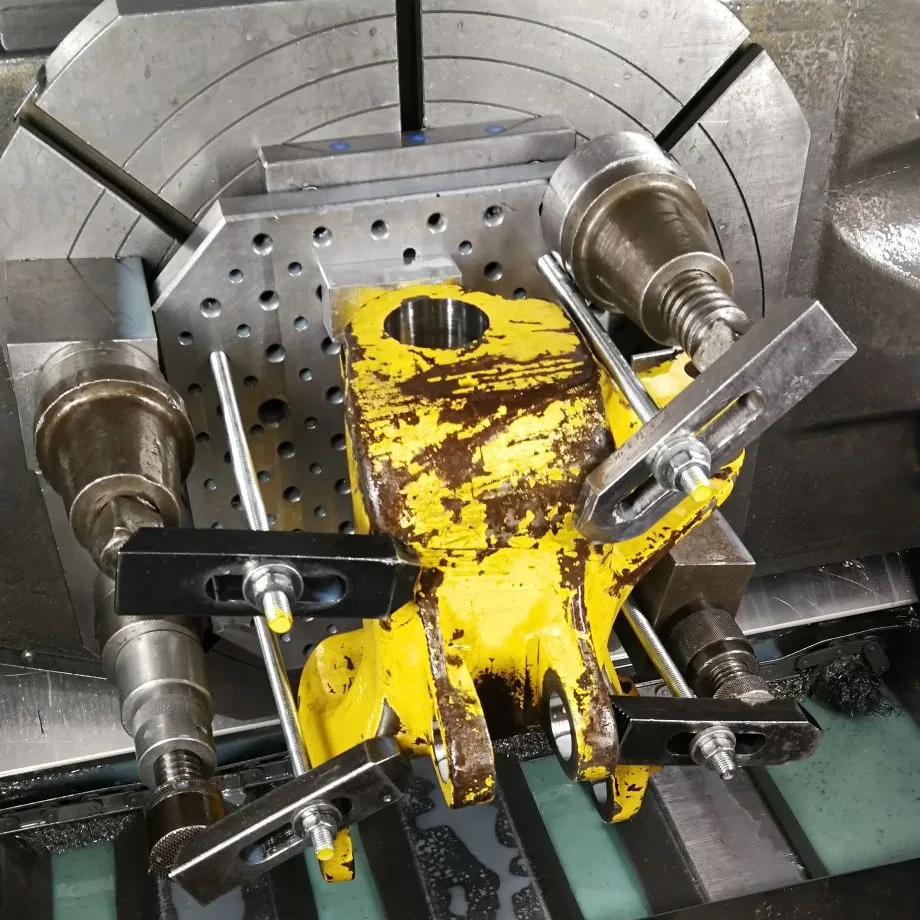
Now this is where we eventually started and asked ourselves how this component would have to be modified and adapted so that it could simply be repaired after a certain amount of wear and tear and people do not always have to procure a new part – which is harmful to the environment in many respects. We sat down with our experts, fiddled around and ultimately fitted the swing frame with replaceable bushings. This way, it is now possible to just insert new bushings into the frame when they are worn out.
Basically just a small change, but with a big effect: The arm mount we have modified is resource and environmentally friendly, sustainable and – a nice side effect – significantly cheaper, because in the future you don’t always have to buy an expensive new part, but just a few small, inexpensive bushings.
It’s a win-win, we would say. 🙂
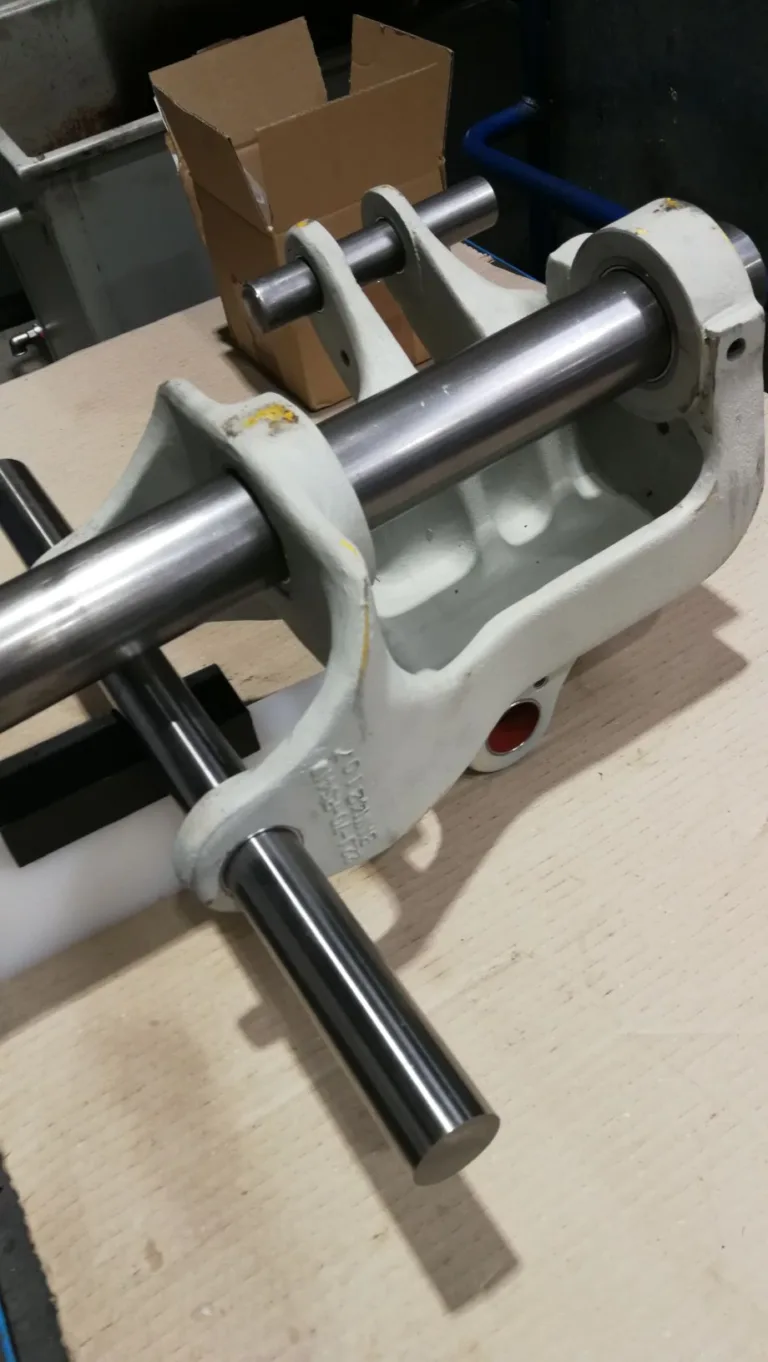
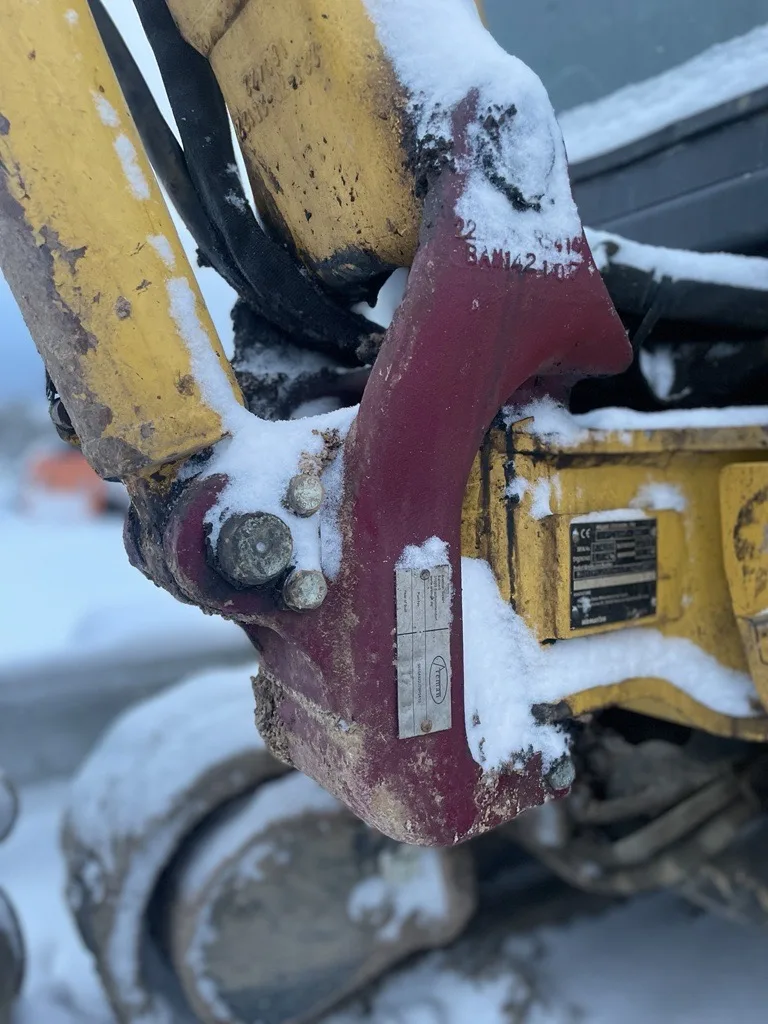
Our optimized swing frame fits the following Komatsu models:
- PC16R-2
- PC16R-3
- PC14R-2
- PC14R-3
In our daily work routine, we are confronted from time to time with situations that virtually “request” a bit of rethinking. Things that have always been done this way and have never really been questioned, but now seem far too laborious and simply no longer right for a variety of reasons. Since the topics of resource conservation and sustainability are close to our hearts, the following case exactly represents such a situation:
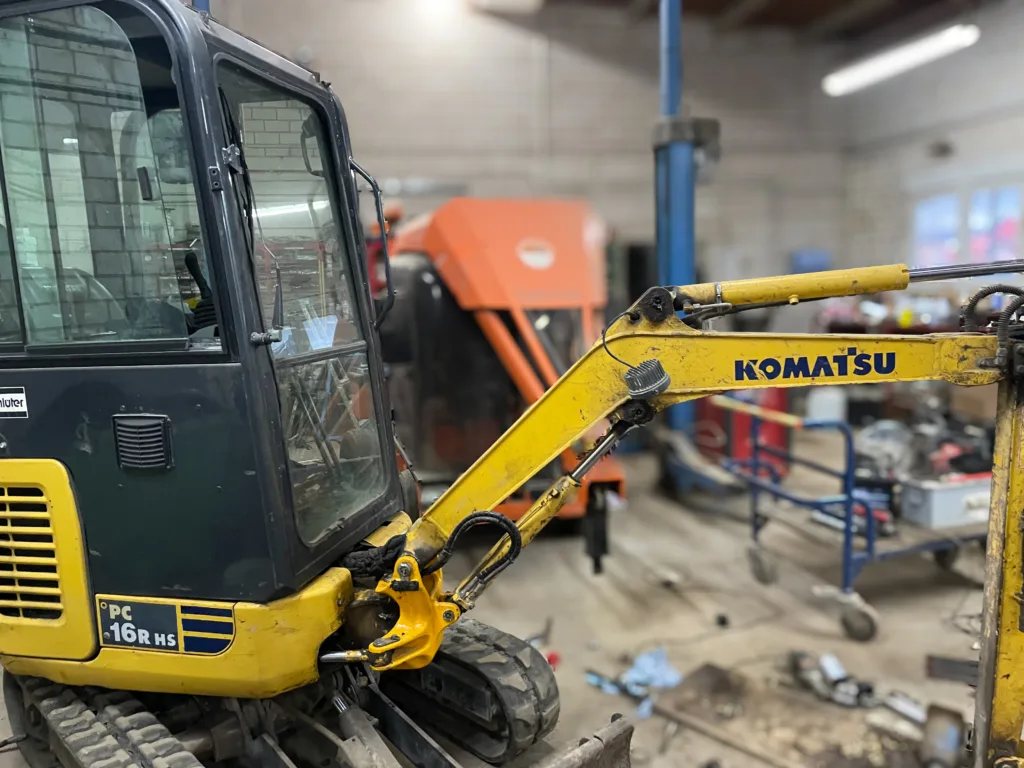
The swing frame of a Komatsu mini-excavator, spare part comparison number 22J-70-R5410, suitable for models PC14 and PC16, was worn out and we were given the task of getting a corresponding spare part. The problem with this – and after all the point that spurred us to action: These components are made in Asia, so they have to be shipped halfway around the world to get to us; they’re made entirely of steel, and one part weighs about 20 kg. So the whole thing is incredibly resource-intensive and ultimately, of course, correspondingly expensive.
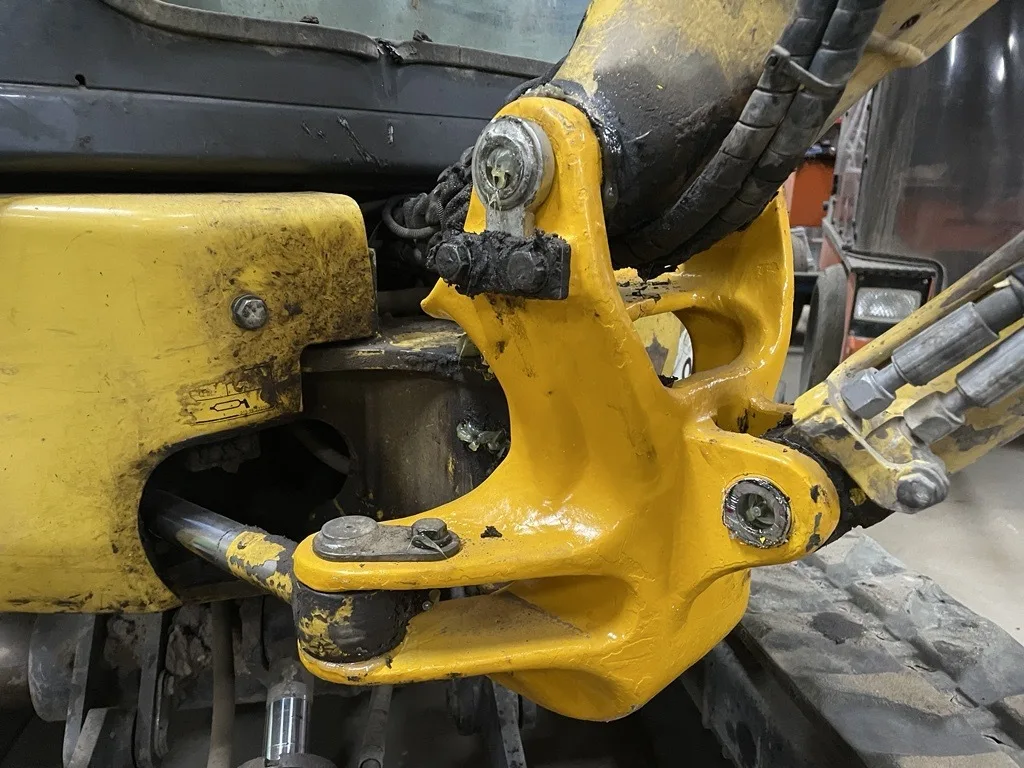
This is why we asked ourselves how this issue could be solved or at least simplified, but were soon faced with the challenge that this part itself cannot be repaired at all, as it consists of one cast-iron piece of steel with holes simply drilled into it. Since the entire boom/arm of the excavator hangs on this mount and it is therefore exposed to a correspondingly high stress, the bushings are worn out after a short time and the part is no longer usable. Result: it has to be replaced.
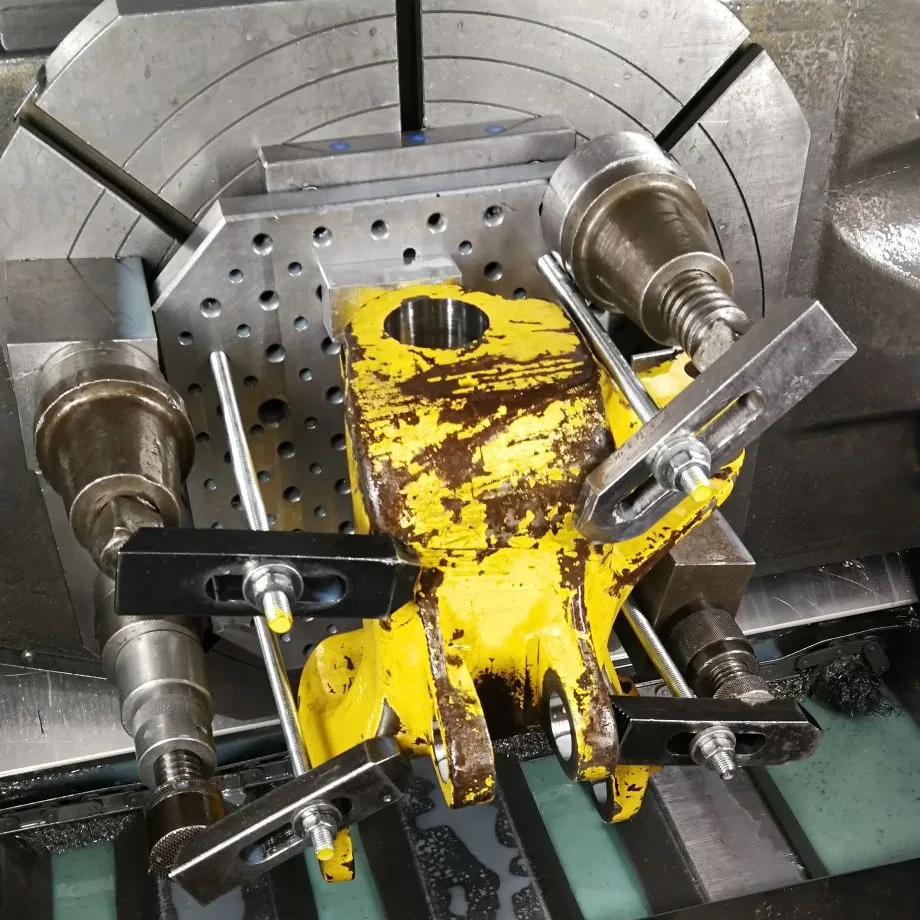
Now this is where we eventually started and asked ourselves how this component would have to be modified and adapted so that it could simply be repaired after a certain amount of wear and tear and people do not always have to procure a new part – which is harmful to the environment in many respects. We sat down with our experts, fiddled around and ultimately fitted the swing frame with replaceable bushings. This way, it is now possible to just insert new bushings into the frame when they are worn out.
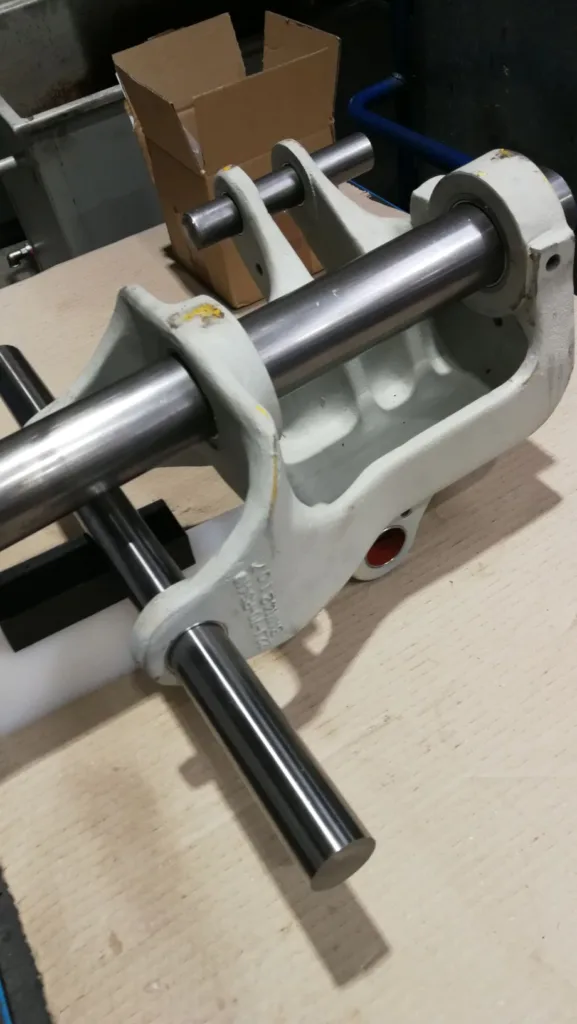
Basically just a small change, but with a big effect: The arm mount we have modified is resource and environmentally friendly, sustainable and – a nice side effect – significantly cheaper, because in the future you don’t always have to buy an expensive new part, but just a few small, inexpensive bushings.
It’s a win-win, we would say. 🙂
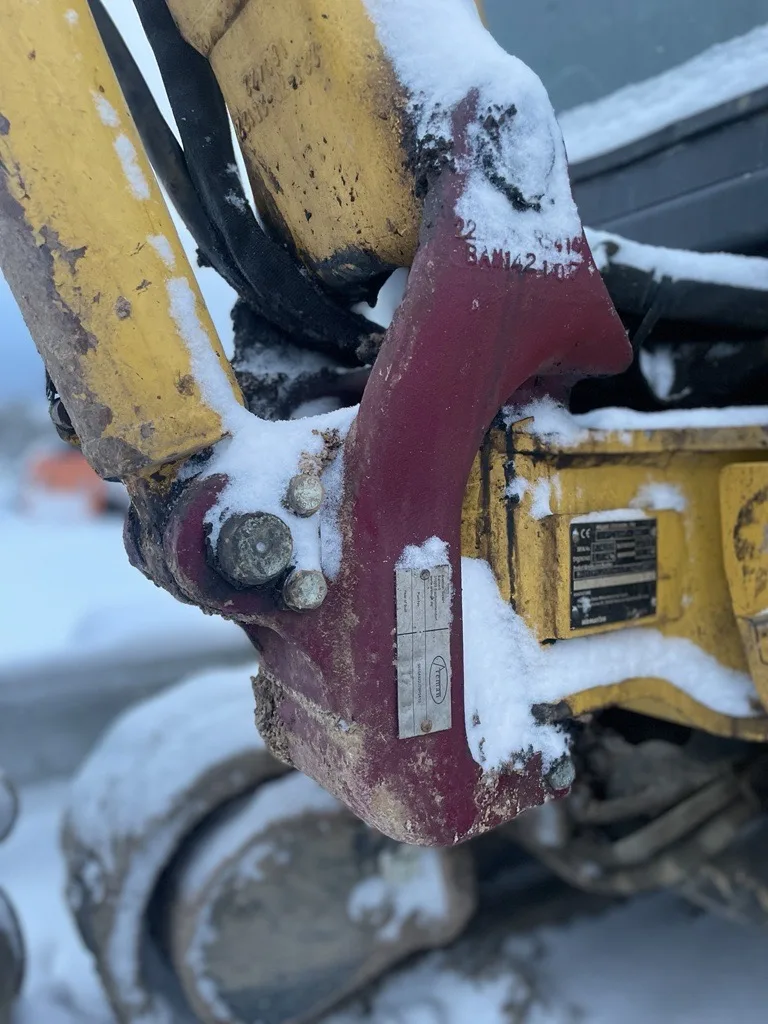
Our optimized swing frame fits the following Komatsu models:
- PC16R-2
- PC16R-3
- PC14R-2
- PC14R-3